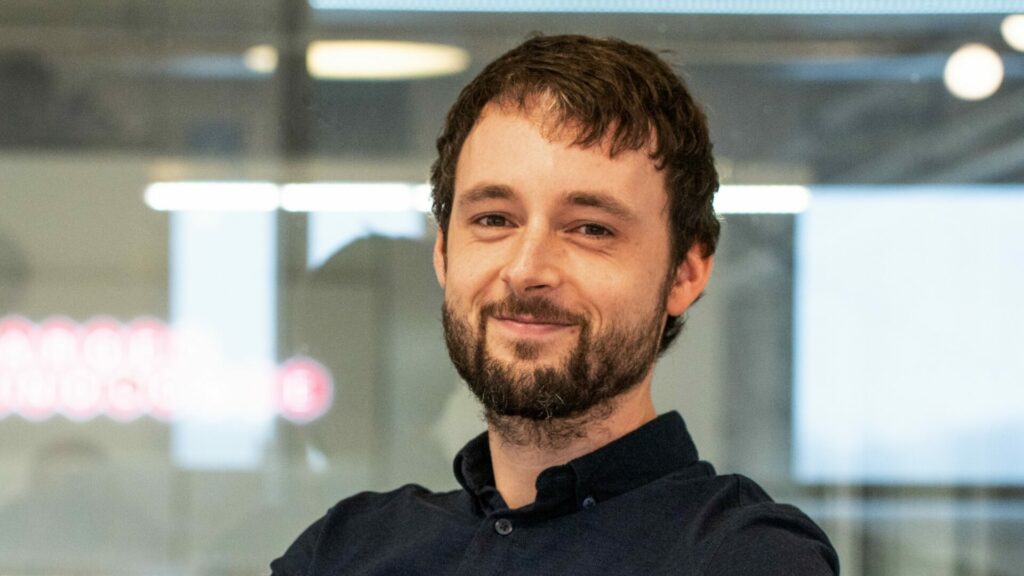
Příprava tohoto zdánlivě jednoduchého procesu trvala několik let, teď se tento unikátní projekt pod názvem Saturnin, za nímž stojí společnost Beneva, úspěšně rozvíjí. Důkazem toho je, že se do něj zapojil i největší tuzemský výrobce automobilů, mladoboleslavská Škoda Auto.
Proč jste se rozhodli právě pro využití ocelového odpadu?
Má to dvě roviny. Tou první je ekologie. Ocelářský průmysl je obecně energeticky extrémně náročný, má velký dopad na životní prostředí. Nejde jenom o oxid uhličitý, který vzniká při výrobě, ale také o další emise anebo o těžbu surovin či dopravu. Obecně prostě dává smysl pokusit se materiál ještě dále využít, aspoň částečně, než se zbytek zrecykluje, a snížit tak dopad na životní prostředí.
A druhá rovina?
Když startuje nějaký byznys, musí to dávat smysl i ekonomicky. To je podle nás stejně silný argument jako ten ekologický. Musím to ale trochu vysvětlit. Principem našeho projektu je, že snažíme identifikovat materiál, který se nevyužívá dostatečně efektivně. Odpad se sice recykluje, ale to znamená, že se znovu roztaví a něco se z něj znovu vyrobí. K tomu je zapotřebí spoustu energie.
My postupujeme tak, že námi vybraný odpad rovnou využijeme k další výrobě. A co je podstatné: Jsme schopni dodat zákazníkovi materiál s výhodnější cenou, než kdyby se odpad recykloval. Vypadává jeden mezičlánek, což představuje nižší dopad na životní prostředí a současně to dává ekonomicky smysl.
Máte dostatek materiálu? Oceli se produkuje obrovské množství, nejen pro automobilový průmysl, i když automotive je obor, který zpracovává nejvíce ocelového plechu. Potenciál je každopádně velký. Podle informací, které máme přímo z automobilek, se ve výsledku až padesát procent materiálu při výrobě karoserie nevyužije, takže se sešrotuje a vrací se do hutě. Každé procento, které se nám podaří ušetřit, se počítá.
Skutečně až padesát procent? Každá firma se přece snaží množství odpadu snižovat.
To máte sice pravdu, ale problémem je, že jejich možnosti jsou poměrně malé, a problém s odpadem řeší jen v rámci své fabriky. Snaží se sice využít co nejvíce nakoupeného plechu, ale v některých případech jim technologie neumožňují množství odpadu snížit ještě více.
Naší výhodou je, že dokážeme propojit více podniků, takže i pravděpodobnost, že najdeme firmu A, jejíž odpad sice není využitelný u stejné firmy, ale může ho využít firma B nebo C, je pak významně vyšší. Čím více subjektů se propojí, tím je potenciál návratu materiálu zpět do výroby větší.
Jak váš projekt přesně funguje?
Na úplném začátku je sběr dat, napřed musíme od automobilek a přidružených výrobních podniků získat sadu poměrně detailních informací: Kolik oceli spotřebují, v jaké jakosti, tloušťce, jestli je pozinkovaná, kolik odpadu vzniká a tak dále.
Důležitá je také logistika, především jak daleko se od sebe jednotlivé podniky nacházejí. Všechna data pak zadáme do našeho počítačového systému a hledáme shodu. Zjistíme tedy, kolik daného dílu by se z odpadní oceli ještě podařilo vystřihnout a komu by se mohl hodit.
To vypadá poměrně jednoduše, ale asi v tom budou různé háčky…
To, co jsem řekl, bylo velmi zjednodušené, ve skutečnosti jde o poměrně sofistikovaný proces, a rozhodně není tak snadný. Ale v principu jde skutečně o to, že náš systém propojí firmu, která má vhodný odpad, z něhož se ještě dá něco vyrobit, s podnikem, který takový díl shání.
Musím ještě poznamenat, že cílíme výhradně na výrobní odpad, nikoli spotřebitelský. Automobilky mají na materiál velmi přísné požadavky, těžko by se daly takto využívat třeba části karoserie z vrakoviště. To už jsou plechy vylisované a mají i několik vrstev laku. My dokážeme automobilkám dodat stoprocentní ekvivalent k materiálu z huti.
Výrobní odpad se už nemusí upravovat před tím, než se znovu vrátí na výrobní linku?
To je jedna z věcí, která není úplně jednoduchá. S takovým materiálem se musí udělat několik věcí. Zaprvé se to musí zkontrolovat všechny jeho parametry. I když je to výrobní odpad, musíme mít absolutní jistotu, že je materiál v pořádku.
V rámci naší skupiny máme i akreditovanou materiálovou laboratoř, takže z každé dodávky odpadu zkoušíme mechanické a chemické parametry, měříme zinkovou vrstvu a tak dále, abychom měli komplexní analýzu materiálu.
Součástí je i kontrola původní dokumentace. Pokud je vše v pořádku, může materiál do výroby, v našem pilotním zařízení v Benátkách nad Jizerou máme vlastní autonomní robotizovanou nástřihovou linku, která plechy uzpůsobí požadavkům zákazníka.
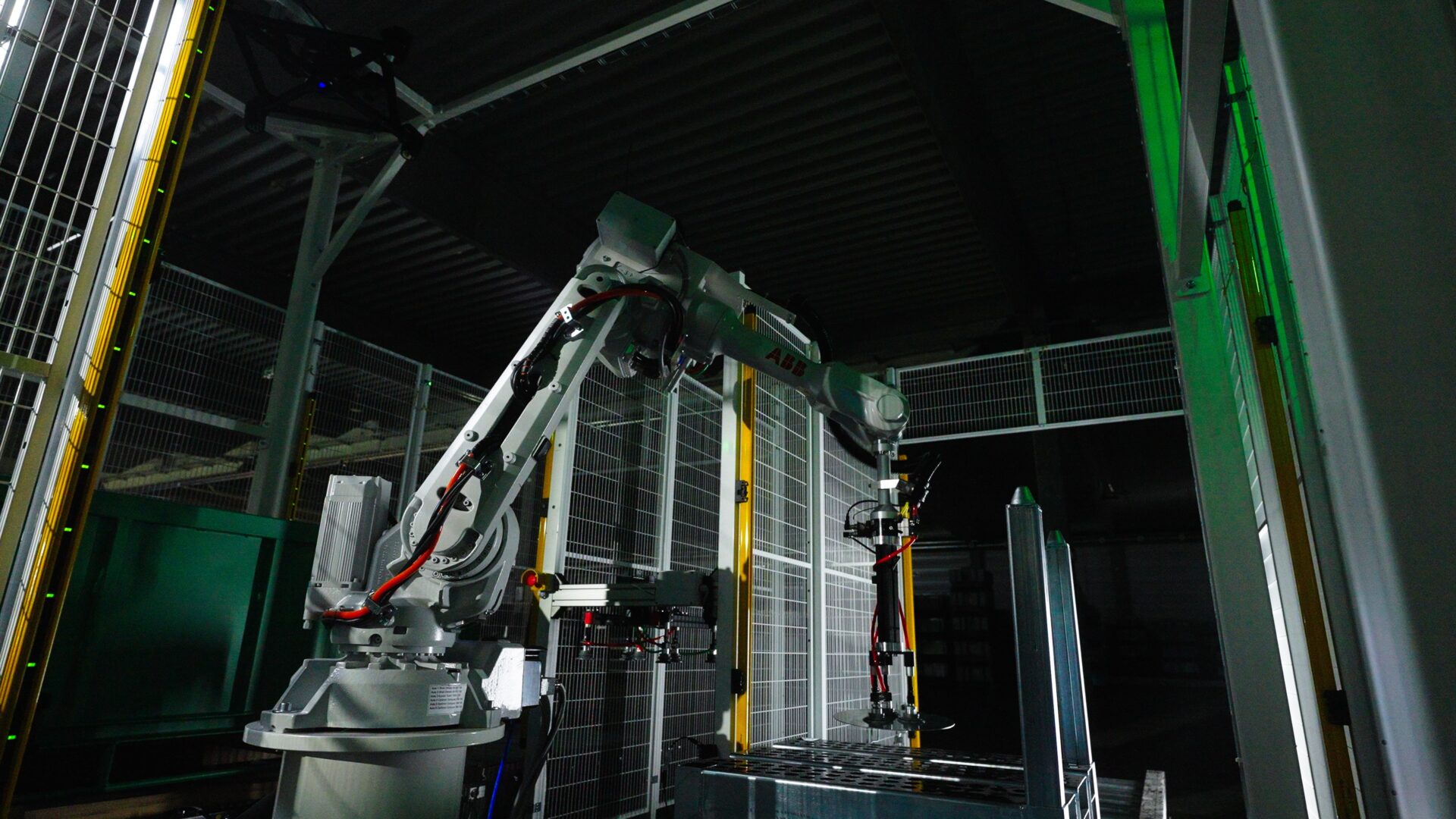
Kolik jich už ve svém systému máte?
V tuto chvíli máme v databázi řádově desítky typů využitelných odpadů o celkovém ročním objemu několika tisíc tun. Ale znovu připomínám, že jsme na úplném začátku. Snažíme se projekt rozšířit všude, kde dává smysl. Plechy vykupujeme za výhodnější cenu, než když se prodávají jako odpad, díky tomu máme větší šanci, že se do našeho systému zapojí více firem.
Druhým benefitem je, že náš projekt nabízí podnikům poměrně zajímavé emisní úspory, které se pak firmám hodí k plnění evropských ekologických požadavků včetně nižší uhlíkové stopy. Můžou si sice koupit „zelenou“ ocel přímo z hutí, ale za takové výrobky jsou obrovské příplatky, řádově jde o desítky procent.
A kolik se vám podaří ušetřit?
Pokud jde o emise, náš materiál vykazuje řádově nižší uhlíkovou stopu v porovnání s konvenčně vyráběnou ocelí. Pokud jde o cenu, odpověď je složitější, protože je silně individuální a ovlivňuje ji mnoho faktorů, jedním z těch zásadních je například procento využití odpadu, z něhož se díl vyrábí. Každá položka je tedy specifická. Musím ale říci, že zatím ve všech případech, kdy jsme zákazníkovi dokázali nahradit jeho materiál naším nízkoemisním, jsme se s cenou dostali dokonce níže.
Podstatné je ještě dodat, že celé to je živá věc. Náš projekt stále posouváme kupředu. Není to tak, že jsme několik let něco vyvíjeli, a teď už to jen budeme provozovat. Dokončili jsme jen první etapu.
Jsme například přesvědčeni, že náš projekt má potenciál i ve vybraných zahraničních státech. Princip výroby karoserie je prakticky všude stejný, používá se stejná technologie, jsou to stejné postupy. Takže není důvod, aby to nefungovalo například v Německu, Francii, ale třeba i ve Spojených státech nebo v asijských zemích s rozvinutým automobilovým průmyslem. Zajímáme se ale také o další obory, kde se zpracovává plech, což může být třeba kovový nábytek, bílé spotřebiče v domácnostech, elektroprůmysl a tak dále. Od počátku byl náš projekt zamýšlený jako globální. Jsme přesvědčeni o tom, že je jen otázkou času, kdy se dostaneme také ven.
Přibývá firem, které se zapojují do vašeho projektu?
Ano, přibývá, i když o přesném počtu bych zatím nemluvil. Ale je pravdou, že máme velmi příznivé ohlasy. Asi můžeme zmínit, že spolupracujeme například s mladoboleslavskou škodovkou, jejich přístup je velmi aktivní a profesionální. Ostatně pro automobilky je hledání udržitelných cest v současnosti hodně důležité. S každou firmou je ale spolupráce individuální.
Jak to bude s dopravou? Z Moravskoslezského kraje to je přece poměrně dálka, a doprava zanechává také emisní stopu.
Samozřejmě pracujeme s tím, že časem budeme budovat i další zpracovatelská centra, kde se budou zpracovávat ocelové plechy z výrobního odpadu k novému využití pro konkrétní automobilku nebo jiný podnik, který o ně bude mít zájem.
Jak velká byla investice do rozjezdu vašeho projektu?
Jsou to vyšší desítky milionů korun. Všechno z privátních zdrojů našich podílníků, nemáme ani korunu ze státních dotací. Jsou to pro někoho možná velké peníze, ale musíte si uvědomit, že jsme museli vyvinout speciální počítačový algoritmus nebo vyvinout a vybudovat autonomní robotizovanou linku. Dneska ale můžeme říct, že se nám podařil vytvořit unikátní systém, na nic podobného jsme ve světě nenarazili.